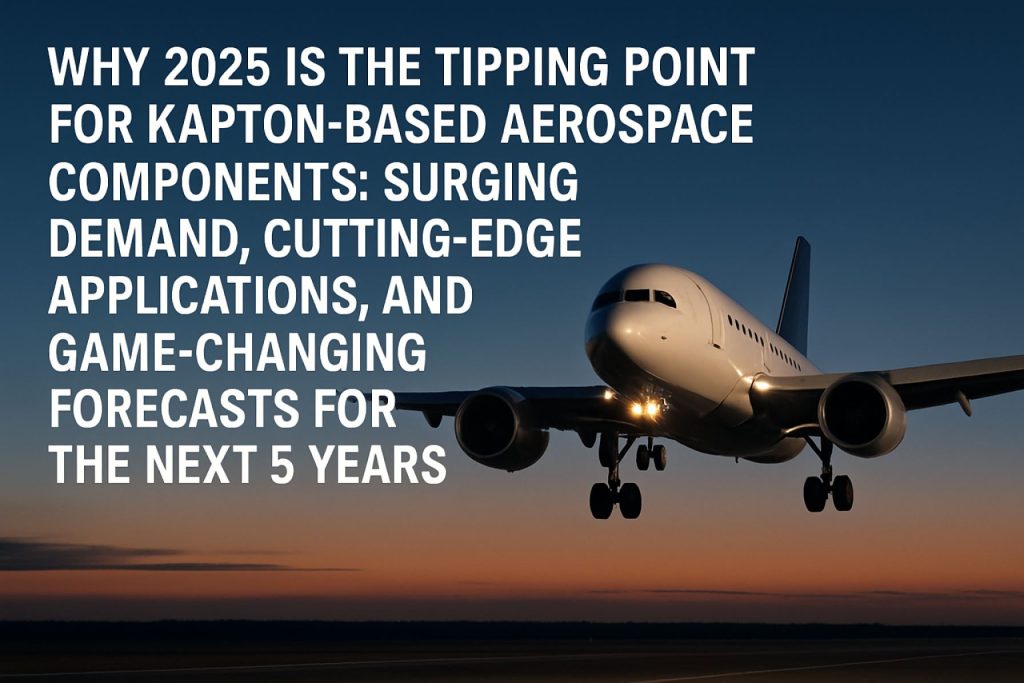
Kapton Aerospace Breakthroughs: 2025–2029 Market Booms & Next-Gen Tech Revealed
Table of Contents
- Executive Summary: The State of Kapton-Based Aerospace Components in 2025
- Market Size, Growth, and 2029 Projections
- Core Properties: Why Kapton Dominates Aerospace Applications
- Emerging Technologies: Advancements in Kapton Films and Composites
- Key Players & Official Industry Initiatives
- Major Aerospace Programs Leveraging Kapton (2025–2029)
- Supply Chain Innovations and Material Sourcing
- Regulatory Standards and Industry Certification Trends
- Competitive Landscape and Strategic Partnerships
- Future Outlook: Disruptive Trends and Market Opportunities through 2029
- Sources & References
Executive Summary: The State of Kapton-Based Aerospace Components in 2025
In 2025, Kapton-based aerospace components are experiencing robust demand and technological advancement, driven by their unique combination of thermal stability, electrical insulation, and lightweight properties. Kapton, a polyimide film developed and produced by DuPont, remains the industry standard for applications where resistance to extreme temperatures and harsh environments are critical, such as spacecraft insulation, flexible printed circuits, and wire wraps.
The aerospace sector’s reliance on Kapton is underscored by its integration into next-generation satellites, launch vehicles, and crewed spacecraft. For instance, NASA continues to utilize Kapton films in multilayer insulation blankets for both orbital and deep-space missions, citing its ability to withstand temperature swings from -269°C to +400°C. In 2025, commercial satellite manufacturers such as Airbus and Northrop Grumman are incorporating Kapton-based flexible circuits and thermal shields to ensure reliability and performance in the harsh space environment.
Production advancements are also notable. DuPont has announced new grades of Kapton film with enhanced dielectric strength and thinner profiles, enabling further miniaturization and weight reduction—key for modern aerospace design. Suppliers such as 3M and TE Connectivity are expanding their Kapton offerings to meet increasing demand for high-performance insulation and masking tapes in both commercial aviation and spaceflight.
In parallel, sustainability and supply security are rising priorities. Aerospace OEMs are collaborating with suppliers to improve the recyclability of Kapton components and to ensure robust supply chains, given the material’s criticality and the growing number of space launches expected through 2030. The ongoing expansion of satellite constellations, lunar exploration initiatives, and reusable launch vehicles further reinforce the outlook for continued growth in Kapton-based component usage.
In summary, the state of Kapton-based aerospace components in 2025 is marked by strong market demand, technical innovation, and strategic initiatives to secure long-term material availability. With leading manufacturers and aerospace organizations investing in new product grades and applications, Kapton’s role in enabling the next era of aerospace engineering is set to deepen over the coming years.
Market Size, Growth, and 2029 Projections
Kapton-based aerospace components continue to experience robust demand due to the material’s exceptional thermal stability, dielectric strength, and chemical resistance—properties critical for the next generation of aircraft and spacecraft. As of 2025, the market for these components is underpinned by growing investments in satellite constellations, commercial spaceflight, and advancements in both civil and military aviation.
Leading manufacturers of Kapton polyimide films, such as DuPont, report increased orders from aerospace OEMs for applications in wire insulation, flexible printed circuits, heater elements, and thermal blankets. DuPont highlights the adoption of Kapton technology in both crewed and uncrewed missions, notably within NASA programs and the rapidly expanding commercial satellite sector.
The satellite industry’s expansion is a key driver, with constellations from operators like SpaceX and OneWeb increasing the demand for lightweight, reliable wiring and thermal management solutions. For instance, TE Connectivity supplies Kapton-insulated wire and cable to satellite manufacturers, emphasizing the material’s role in reducing weight while maintaining performance in extreme environments.
The proliferation of electric and hybrid-electric aircraft programs is also accelerating market growth. Companies such as SABIC and DuPont are expanding their Kapton-based product portfolios to address the insulation and electronics needs of next-generation propulsion systems, which require materials that withstand higher voltages and temperatures.
Looking ahead to 2029, the market outlook remains positive. The continued rollout of low-Earth orbit (LEO) satellite networks, renewed lunar and Mars missions, and the electrification of aviation are expected to sustain double-digit annual growth rates for Kapton-based aerospace components. Major suppliers are investing in capacity expansions and process improvements to meet this rising demand. For example, DuPont announced new investments in Kapton production lines to support aerospace sector requirements.
In summary, the 2025–2029 period is projected to see sustained growth in the Kapton-based aerospace component market, driven by satellite deployment, advanced aircraft, and space exploration programs, with established manufacturers scaling up to ensure reliable supply for mission-critical applications.
Core Properties: Why Kapton Dominates Aerospace Applications
Kapton, a polyimide film developed by DuPont, has established itself as a critical material for aerospace components due to its unique combination of thermal, electrical, and mechanical properties. As the aerospace sector advances into 2025 and beyond, the demand for components that can withstand extreme operational environments continues to rise, reinforcing Kapton’s dominance.
A primary reason for Kapton’s prominence is its extraordinary thermal stability. It remains stable in temperatures ranging from -269°C to +400°C, enabling its use in both cryogenic space missions and high-temperature engine compartments (DuPont). Its low outgassing characteristics meet the strict contamination requirements for satellites and deep-space probes, making it a material of choice for thermal blankets, flexible printed circuits, and wire insulation.
Electrically, Kapton offers high dielectric strength, crucial for the miniaturization and reliability of aerospace electronics. Its robustness helps reduce component failure rates in avionics, satellites, and onboard computers. For instance, the National Aeronautics and Space Administration (NASA) has repeatedly used Kapton films in space probes and Mars rovers to insulate and protect sensitive wiring and circuitry from harsh environments.
Mechanically, Kapton boasts remarkable tensile strength and flexibility, allowing it to be fabricated into thin, lightweight films that do not add significant mass to spacecraft—a critical design factor for both commercial and defense aerospace manufacturers. The ongoing shift toward electric propulsion and compact satellite designs in 2025 has increased reliance on Kapton-based flexible circuits and cable harnesses (DuPont).
Looking ahead, the integration of Kapton in new-generation aerospace systems is expected to accelerate. Leading suppliers such as DuPont and 3M continue to develop advanced Kapton variants with enhanced flame-retardancy and tailored dielectric properties, supporting the evolving needs of hybrid-electric aircraft and high-performance satellites. With the proliferation of small satellites and increased space mission frequency projected through the late 2020s, Kapton’s role as the backbone material for reliable, lightweight, and durable aerospace components is set to expand further.
Emerging Technologies: Advancements in Kapton Films and Composites
Kapton polyimide films and composites are at the forefront of innovation in aerospace component engineering, driven by their exceptional thermal stability, chemical resistance, and mechanical properties. In recent years, manufacturers have accelerated the development of advanced Kapton-based materials to meet the evolving demands of next-generation spacecraft, satellites, and aircraft. In 2025, these advancements are particularly evident in several key application areas, with a strong emphasis on miniaturization, durability, and multifunctionality.
A notable trend is the integration of ultra-thin Kapton films into flexible printed circuits (FPCs) and multilayer insulation (MLI) blankets. These components are critical for thermal management in spacecraft and satellites, where weight and performance are paramount. DuPont, a principal producer of Kapton, has introduced new formulations with enhanced dielectric properties and improved outgassing characteristics, specifically targeting aerospace mission requirements through 2025 and beyond. These films are now being used in the latest generation of CubeSats and deep space probes, reducing overall system mass while maintaining robust electrical insulation.
Advancements in Kapton composites are also enabling the production of lightweight structural components, such as honeycomb panels and composite laminates. Teijin has developed Kapton-reinforced composite solutions that combine polyimide film with high-performance fibers, resulting in components that can withstand extreme temperature cycles and mechanical stress. These materials are being evaluated for next-generation aircraft interiors and for structural parts in reusable launch vehicles, reflecting a growing industry focus on sustainability and reusability.
Electronics manufacturers such as DuPont and Rogers Corporation are also incorporating Kapton in advanced tape and cable insulation systems, which are essential for high-density power distribution and signal transmission in satellites and unmanned aerial vehicles (UAVs). These solutions offer improved flexibility and reliability, particularly in the harsh conditions of low earth orbit (LEO) and deep space missions.
Looking ahead, the outlook for Kapton-based aerospace components remains robust. Manufacturers are investing in nanostructured Kapton composites and hybrid materials to further reduce weight and enhance multifunctionality, such as integrating sensing or EMI shielding directly into the film. As space and aviation missions demand higher performance under more extreme conditions, the role of advanced Kapton films and composites is set to expand rapidly through the next several years, solidifying their status as essential materials in aerospace innovation.
Key Players & Official Industry Initiatives
Kapton polyimide films, celebrated for their high thermal stability, electrical insulation, and radiation resistance, have become integral to aerospace engineering. As of 2025, a select group of manufacturers and industry organizations are driving forward the development and implementation of Kapton-based components in both commercial and defense aerospace sectors.
- DuPont remains the primary innovator and supplier of Kapton materials. In recent years, DuPont has expanded its Kapton film portfolio, introducing grades tailored for extreme aerospace environments, such as Kapton® FPC and Kapton® RS, which offer enhanced electrical conductivity and mechanical robustness for satellite and avionics applications. The company’s collaborations with satellite manufacturers and space agencies continue to set industry benchmarks for reliability and safety.
- 3M is another key player, offering a range of Kapton-based tapes and laminates used in wire and cable insulation, thermal shielding, and sensor protection for aerospace electronics. 3M’s recent product developments focus on increasing adhesive performance and longevity in high-vibration, high-altitude environments, addressing evolving requirements in urban air mobility and next-generation aircraft.
- Saint-Gobain has advanced Kapton-based flexible heaters and insulation solutions, notably for de-icing systems and thermal management in aircraft and spacecraft. Saint-Gobain is partnering with OEMs to deliver custom-engineered components for electric vertical takeoff and landing (eVTOL) vehicles and new satellite platforms.
- NASA continues to set standards for the use of Kapton in spaceflight. Its ongoing Artemis program and lunar surface systems incorporate Kapton in thermal blankets, solar arrays, and wiring assemblies. NASA regularly updates guidelines for material selection and testing, thereby influencing aerospace component suppliers worldwide.
- Airbus and Boeing have each expanded their use of Kapton-based wire insulation and structural laminates to improve aircraft weight, reliability, and fire performance. Airbus and Boeing both emphasize the importance of advanced materials in their sustainability roadmaps and are engaged in joint initiatives with suppliers to trial next-generation Kapton variants.
Looking forward, official industry initiatives—such as those led by the SAE International—are establishing standardized testing and qualification protocols for Kapton-based aerospace parts. As electrified propulsion, reusable launch vehicles, and satellite constellations proliferate through the late 2020s, Kapton’s role is expected to grow, underpinned by the continued investments and collaborative R&D efforts of these key industry players.
Major Aerospace Programs Leveraging Kapton (2025–2029)
As the aerospace sector continues its push for lighter, more durable, and thermally robust materials, Kapton-based components are increasingly central to the design and operation of major aerospace programs. Kapton polyimide films, developed and manufactured by DuPont, offer exceptional thermal stability, electrical insulation, and chemical resistance—qualities that make them indispensable in modern spacecraft, satellites, and aircraft. The period from 2025 through 2029 is set to witness intensified integration of Kapton-based solutions across several high-profile aerospace programs.
- Boeing Commercial and Defense Aircraft: Boeing continues to utilize Kapton films and wires for wire insulation, flexible printed circuits, and thermal blankets in its commercial and defense aircraft. These components are valued for their weight savings and ability to withstand high operating temperatures, contributing to improved aircraft efficiency and reliability. With Boeing’s forecast to ramp up production of its 737 and 787 lines through 2025–2029, demand for Kapton-based components is expected to rise accordingly.
- NASA Artemis Lunar Missions: The Artemis program, led by NASA, relies on Kapton for thermal control blankets, solar array substrates, and insulation on its Orion spacecraft and lunar gateway modules. Kapton’s proven performance in the extreme conditions of space ensures the protection of critical avionics and structural elements. As Artemis missions intensify toward lunar landings and the construction of a sustainable lunar presence, the use of Kapton materials is set to expand further.
- ESA Earth Observation and Science Satellites: The European Space Agency (ESA) employs Kapton films in the construction of multi-layer insulation (MLI) blankets and flexible circuit boards for satellites such as Copernicus and the upcoming Earth Explorer missions. With several launches scheduled between 2025 and 2029, ESA’s reliance on Kapton for thermal management and electronics protection will remain pivotal.
- SpaceX Starship and Starlink Programs: SpaceX incorporates Kapton-based insulation and circuit materials in both its Starship vehicles and Starlink satellites. The large-scale deployment of Starlink satellites and the expansion of Starship missions over the next few years underscore the need for durable, lightweight materials that can withstand the harsh environment of space.
Looking ahead, advancements in Kapton processing and composite integration are anticipated to further enhance the performance and application range of these materials in aerospace. Leading manufacturers such as DuPont and system integrators are investing in new formulations and manufacturing techniques, supporting the next generation of aerospace innovation.
Supply Chain Innovations and Material Sourcing
The supply chain for Kapton-based aerospace components is experiencing significant transformation in 2025, driven by the aerospace industry’s focus on resilience, traceability, and sustainability. Kapton, a polyimide film produced primarily by DuPont, remains a critical material for thermal insulation, flexible circuits, and other high-performance applications in spacecraft and aircraft. Recent disruptions—ranging from global logistics constraints to increased demand from satellite constellations—have accelerated innovation throughout the supply chain.
To address material sourcing challenges, major aerospace suppliers are diversifying procurement strategies. DuPont has continued to expand its production capacity and enhance quality controls, ensuring consistent supply for aerospace-grade Kapton films. Downstream component manufacturers, such as Zeus Industrial Products and TE Connectivity, are increasingly collaborating with material producers to co-develop custom Kapton-based solutions tailored for next-generation airframes, satellites, and hypersonic vehicles. These partnerships are fostering greater transparency in raw material sourcing and allowing for rapid adaptation to changing specifications.
In 2025, digital supply chain management has become a cornerstone for both material and component providers. Companies are implementing advanced traceability systems, including RFID tagging and blockchain-based provenance tracking, to ensure the authenticity and aerospace compliance of every Kapton batch. Safran has reported success integrating such solutions within its thermal protection material supply chains, enhancing both regulatory compliance and customer confidence.
Sustainability is also influencing sourcing strategies. Manufacturers are investigating closed-loop recycling for polyimide films, reducing waste and dependence on virgin materials. For instance, DuPont has announced ongoing research into reclaiming and reprocessing Kapton from end-of-life aerospace components. Furthermore, aerospace primes are favoring suppliers that can demonstrate reduced environmental footprints, pushing the industry toward greener production and logistics.
Looking ahead to the next few years, these innovations are expected to further stabilize the supply of Kapton-based aerospace components. As new satellite mega-constellations and commercial spaceflight projects ramp up, the sector’s ability to deliver high-reliability materials will hinge on the continued evolution of supply chain transparency, digitalization, and sustainable sourcing.
Regulatory Standards and Industry Certification Trends
As the aerospace industry evolves to accommodate more stringent safety, environmental, and performance requirements, regulatory standards and certification processes for Kapton-based components are under continuous development. Kapton, an aromatic polyimide film manufactured by DuPont, is widely used in aerospace applications due to its exceptional thermal stability, electrical insulation, and resistance to radiation and chemicals. In 2025 and the coming years, its use is increasingly shaped by regulatory scrutiny and industry-wide certification initiatives.
Regulatory bodies such as the Federal Aviation Administration (FAA) and the European Space Agency (ESA) have updated protocols governing the use of high-performance polymers like Kapton in aircraft wiring, thermal blankets, and flexible circuit applications. The FAA’s ongoing Special Airworthiness Information Bulletins (SAIBs) emphasize the need for compliance with updated flammability, smoke, and toxicity (FST) criteria, particularly in commercial and next-generation electric aircraft. The European Union Aviation Safety Agency (EASA) is also harmonizing its material standards to closely align with the latest SAE International and ASTM International testing protocols, focusing on the long-term reliability and environmental performance of polymeric materials.
In 2025, manufacturers such as DuPont and leading aerospace suppliers like TE Connectivity are investing in enhanced traceability and robust quality management systems. This includes digital certification processes that support real-time material tracking and documentation to ensure compliance throughout the supply chain. These companies are increasingly participating in industry-wide consortia to standardize Kapton component testing, focusing on durability under extreme thermal cycles and exposure to space environments.
Looking ahead, several trends are expected to shape certification processes. The development of new Kapton grades with improved FST characteristics is anticipated to facilitate broader acceptance in both civilian and military aerospace applications. Industry groups, such as the Aerospace Industries Association (AIA), are working with regulators to streamline the adoption of next-generation insulation materials by promoting harmonized international standards. Additionally, space agencies are collaborating on certification frameworks that address the unique demands of satellite and deep-space missions, where Kapton’s properties are critical.
These efforts collectively aim to ensure that Kapton-based aerospace components not only meet but exceed evolving regulatory requirements, supporting industry innovation while maintaining the highest levels of safety and reliability in flight and space operations.
Competitive Landscape and Strategic Partnerships
The competitive landscape for Kapton-based aerospace components in 2025 is characterized by robust activity among established material suppliers, aerospace manufacturers, and strategic partnerships aimed at leveraging Kapton’s unique properties for next-generation applications. DuPont, the originator of Kapton polyimide film, remains the industry leader, continuously innovating in high-performance films tailored for space and aviation environments. Their Kapton films are integral in spacecraft insulation, flexible printed circuits, and thermal blankets, with recent advancements focusing on improved radiation resistance and lower outgassing for deep space missions.
In parallel, 3M continues to expand its portfolio of polyimide tapes and films, targeting applications in satellite shielding, cable harnessing, and electronic assembly for both commercial and defense aerospace projects. 3M’s collaborations with satellite manufacturers and avionics suppliers in 2024–2025 are driving the development of custom Kapton solutions that address the growing demand for lightweight and reliable materials in low-Earth orbit (LEO) and lunar missions.
European suppliers such as DuPont (with significant operations in the EU) and SABIC are also investing in R&D to meet the stringent requirements of the European Space Agency (ESA) and other regional aerospace entities. SABIC has announced new initiatives for high-performance film development, emphasizing sustainability and recyclability, which are increasingly important in the aerospace supply chain as environmental standards tighten.
Strategic partnerships are shaping the industry, with OEMs and Tier 1 suppliers collaborating closely with material innovators. For instance, Lockheed Martin has partnered with material providers for the Artemis program’s Orion spacecraft, specifying Kapton-based multi-layer insulation for thermal management in deep space. Similarly, NASA continues to engage with both domestic and international suppliers to source advanced Kapton films for solar sail and satellite applications, reflecting a trend toward cross-continental technology transfer and supply chain integration.
- Companies are forming joint ventures and R&D alliances to accelerate the adoption of next-generation Kapton variants, with a focus on nano-enhanced films and embedded sensor technologies.
- Supply chain resilience is a major strategic priority, leading to regional diversification of production and sourcing, particularly in response to geopolitical uncertainties and increased aerospace activity in Asia.
- Looking ahead, the competitive landscape is expected to see further consolidation and collaboration, as aerospace primes demand integrated solutions and long-term supply agreements for critical missions through 2026 and beyond.
Future Outlook: Disruptive Trends and Market Opportunities through 2029
The outlook for Kapton-based aerospace components over the next five years is characterized by strong innovation, increased adoption in advanced platforms, and expanding market opportunities driven by evolving industry requirements. Kapton’s unique combination of thermal stability, chemical resistance, and lightweight performance continues to drive its integration in critical aerospace applications, from satellites to next-generation airframes.
In 2025 and beyond, the rising deployment of small satellites and high-throughput satellite systems is a key driver for Kapton demand. Kapton films are widely used for flexible printed circuits, insulation, and thermal blankets in satellite manufacturing. Companies like DuPont, the primary producer of Kapton, have reported increased collaborations with satellite manufacturers to optimize Kapton grades for extreme thermal cycling and radiation resistance, supporting the miniaturization trend in space hardware. Additionally, TE Connectivity continues to integrate Kapton in lightweight cabling and harnesses, reducing mass and improving fuel efficiency for both commercial and military aircraft.
Disruptive trends through 2029 include the integration of Kapton-based materials in electric propulsion systems and urban air mobility (UAM) vehicles. As electric vertical takeoff and landing (eVTOL) aircraft programs ramp up, manufacturers are seeking materials that can provide high dielectric strength in compact, harsh environments. DuPont has highlighted R&D efforts focused on enhancing the corona resistance and mechanical flexibility of Kapton films for these emerging applications. Similarly, 3M is advancing multilayer Kapton insulation tapes tailored for high-voltage aerospace power systems, aiming to address the reliability and safety needs of electric aviation.
Another opportunity lies in additive manufacturing and smart structures. The ongoing development of printable Kapton inks and 3D-formed components by companies like DuPont and 3M opens new possibilities for embedding sensors and circuits directly into composite structures, enabling real-time health monitoring and reduced assembly complexity.
Looking to 2029, the growing emphasis on sustainability and lifecycle management in the aerospace industry is expected to further boost demand for Kapton. Its durability, recyclability potential, and ability to withstand multiple mission cycles align with industry goals for greener, longer-lasting aerospace solutions. With major aerospace OEMs and suppliers investing in advanced Kapton technologies, the market is poised for robust growth and continuous innovation over the next several years.